Preparation of steel for galvanizing is a key factor for controlled zinc consumption and best quality of coating.
Galvanizing is possible with only hydrochloric acid and molten zinc, but every step added to these two steps will enhance the quality and decrease the cost of galvanizing. We are repeating this sentence, as it is a crucial one.
The steel before reacting with molten zinc:
- must be free of oil, grease
- must be free of oxides
- must have a smooth surface, as much as possible,
- must have a thin initial layer of zinc coating on it
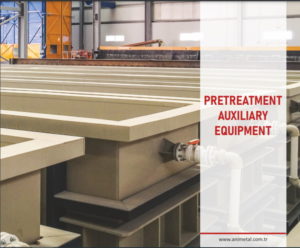
Pretreatment of Steel for Hot Dip Galvanizing
The cost of pretreatment chemicals in the galvanizing process is around 4-7% of the total cost. But the efficiency of the pretreatment on the cost of the galvanizing can be much more than that.
If proper chemicals are not used, or the correct pretreatment steps are not followed; galvanizer may face with an increase in galvanizing cost, about 2-3 times more than the money spent on chemicals. A bad degreaser may increase the zinc ash formation, or a weak inhibitor may increase the dross formation significantly; ending with an 0,5% increase in total zinc consumption.
Zinc consumption should be controlled since it has the biggest influence on the cost. Pretreatment is one of the key steps of the galvanizing process to control the zinc consumption.
You can also access our article titled “History of Hot dip Galvanizing” or to get more information about our hot dip galvanizing factory equipment by clicking the links.
ANI METAL is one of the leading plant suppliers in hot dip galvanizing industry, provides supply of turnkey galvanizing plants and engineering supports as well. Contact now to get more information!