Manual Semi Automatic or Fully Automatic Plants?
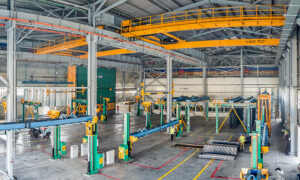
Manual Semi Automatic or Fully Automatic Plants
Table of Contents
Understanding Hot-Dip Galvanizing Plant Configurations
There are numerous hot-dip galvanizing plants all over the world. Depending on the level of automation, hot-dip galvanizing plants can be categorized into three types: manual, semi-automatic, and fully automatic. Each configuration has its own advantages and applications.
Manual Hot-Dip Galvanizing Plants
In a manual hot-dip galvanizing plant, all processes are controlled and executed by operators. The steel articles are manually transferred through the pre-treatment baths, drying, zinc bath, and post- treatment processes. The immersion and withdrawal times, as well as other critical parameters, are dependent on the operator’s experience and skill level. The primary advantage of a manual plant is its low initial investment and operational flexibility. However, reliance on operators introduces a degree of variability, which can lead to differences in coating thickness, and potential over- or under-processing of steel articles in general.
Semi-Automatic Hot-Dip Galvanizing Plants
Semi-automatic systems introduce a level of automation that improves process consistency while retaining some manual intervention. In semi-automatic plants, the crane system may automatically handle material movement through the pre-treatment, drying, galvanizing, and post-treatment stages. However, loading the cranes with jigs, and unloading the jigs from the cranes are still performed manually by an operator.
One of the main advantages of a semi-automatic plant over a manual plant is the precise control of immersion times in the pre-treatment baths. This automation eliminates variabilities related to immersion duration, ensuring that the steel is properly prepared before galvanizing. With more efficiency, also comes greater production capacity.
Fully Automatic Hot-Dip Galvanizing Plants
A fully automatic hot-dip galvanizing plant expands upon the automation of a semi-automatic system. In this setup, the crane system autonomously picks up the loaded jigs, transports them through all processing stages, and deposits the finished galvanized products in the designated unloading area. The only manual tasks required in this configuration are loading steel components onto the jigs before processing and unloading the galvanized components afterward.
This represents the highest point of automation a hot-dip galvanizing plant will reach. A fully automatic hot-dip galvanizing process enables galvanizing capacities much higher than that of manual plants. On the other hand, these advantages come with a higher initial investment compared to manual and semi-automatic configurations.
Cost Considerations
From a financial standpoint, manual galvanizing plants are considered the most budget-friendly option, primarily due to their minimal infrastructure requirements and the complete absence of complex automation systems. These systems rely heavily on manual labor, which helps keep the initial investment costs low, making them a viable choice for businesses that prioritize affordability over automation. On the other hand, semi-automatic systems introduce an additional layer of automation, particularly in the form of crane-assisted material handling and process control, which naturally necessitates a greater financial commitment. While this added investment increases the overall capital expenditure, it also enhances process efficiency and reduces the dependency on manual intervention.
In contrast, fully automatic galvanizing plants represent the most capital-intensive option due to their extensive use of automation technology and advanced control mechanisms, which work in harmony to optimize every stage of the galvanizing process. These highly sophisticated systems require substantial upfront investment but provide unparalleled efficiency, consistency, and operational reliability.
Selecting the most appropriate hot-dip galvanizing plant configuration is a decision that hinges on several critical factors, including the available budget, the expected production volume, and the level of process consistency required. Manual systems offer the advantage of flexibility at a relatively lower cost, but they also demand highly skilled operators who can ensure that every step of the process is executed correctly to achieve the desired quality. In contrast, semi-automatic plants enhance process stability by automating key steps such as pre-treatment durations, although they still require a degree of manual oversight to maintain efficiency.
At the highest level of automation, fully automatic plants minimize human involvement to the greatest extent possible, allowing businesses to achieve superior levels of process control, repeatability, and production efficiency. By eliminating variations introduced by human intervention, these systems ensure a consistently high-quality output, making them ideal for large-scale industrial applications where precision and efficiency are of utmost importance. A comprehensive understanding of these different configurations enables businesses to make well-informed decisions when selecting the most suitable system that aligns with their operational goals and financial constraints.