Galvanizing Kettle

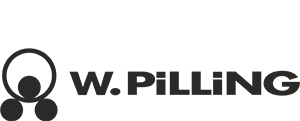
W. Pilling of Riepe, Germany, the world’s leading kettle manufacturer
since
Deepest Kettle of the World
13 x 1,8 x 4,6m
Galvanizing Kettle Brochure
We proudly represent W. Pilling in Tunisia, Algeria, Iraq, Afghanistan, and Turkey. W. Pilling, based in Riepe, Germany, has been the world’s leading kettle manufacturer since 1873. The galvanizing kettles provided by W. Pilling are renowned for their unmatched quality and precision. Below are the key technical specifications and services associated with these kettles:
- Unique Steel Plate Composition:
C: 0,08% – Si: 0,02% – Mn: 0,5% – P: 0,15% – S: 0,01% max.
This carefully engineered steel blend ensures enhanced durability, resistance to corrosion, and optimal performance under high temperatures. - Electro-Slag Welding Technology: This advanced welding technique ensures exceptional strength and durability in kettle construction, minimizing the risk of fatigue and wear over time. It guarantees a robust structure that can withstand the demanding conditions of continuous molten zinc exposure.
- Hot Rolled Steel Sheets: By using hot-rolled steel sheets, W. Pilling reduces production stresses, which significantly extends the kettle’s lifespan. This material choice enhances the kettle’s resistance to thermal expansion and contraction, helping it perform reliably over years of operation.
- No Horizontal or Corner Weldings: The absence of horizontal or corner welds enhances the structural integrity of the kettle, preventing weak points and minimizing the risk of potential leaks or damage during the galvanizing process. This design feature contributes to a more durable and longer-lasting kettle.
- Ultrasonic Testing: W. Pilling uses ultrasonic testing to monitor the thickness of the kettle at various points, providing real-time data on its performance. This technology allows us to predict the kettle’s remaining service life under current operating conditions, ensuring proactive maintenance and avoiding unexpected failures.
- Zinc Pump Out Service: By transferring molten zinc into W. Pilling’s specialized Zinc Holding Containers, the kettle change process is significantly faster and more efficient. This minimizes downtime and ensures that your operation can continue with minimal interruptions.
Table of Contents
Understanding the Importance of the Galvanizing Kettle
In the realm of metal protection, the galvanizing kettle is the cornerstone of the hot-dip galvanizing process. This critical piece of equipment immerses metal items into molten zinc, forming a strong, corrosion-resistant coating. Thanks to W. Pilling’s unique steel formulation and advanced welding technology, their kettles are designed to last significantly longer compared to those of other manufacturers, especially when maintained under optimal conditions such as precise temperature control and regular maintenance.
Using a high-quality galvanizing kettle is essential to minimize the risk of production interruptions caused by equipment failure. A reliable kettle ensures consistent coating quality, reduces downtime, and keeps operations running smoothly without unexpected issues.
Precise Temperature Control for Optimal Results
Temperature control is a crucial factor in the galvanizing process. The kettle must maintain a temperature of approximately 450°C (842°F) to ensure the proper adhesion of the zinc coating to the metal. Overheating can cause excessive wear on the kettle walls, significantly shortening its lifespan. Therefore, maintaining the right temperature is essential not only for quality but also for the longevity of the kettle itself.
Essential Maintenance for Longevity and Efficiency
To ensure the galvanizing kettle performs at its best over time, regular maintenance is vital. Routine inspections should be carried out to identify any signs of wear or corrosion. Regular cleaning of dross and side ashes is crucial to remove residue and impurities that could affect the quality of the zinc coating. This also helps to prevent localized overheating, which can lead to wear and leaks in the kettle. By addressing these issues proactively, the kettle’s performance is optimized, and its lifespan is extended.
In summary, maintaining a high-quality galvanizing kettle and following proper temperature control and maintenance protocols is key to achieving consistent results and ensuring long-term operational success. By choosing W. Pilling’s advanced kettles, you invest in reliability, efficiency, and durability for your galvanizing operations.
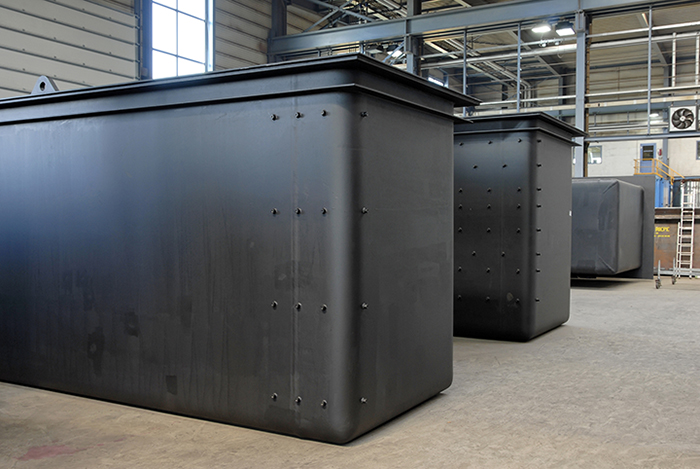
Galvanizing Kettle – Hot Dip Galvanizing | ANI METAL
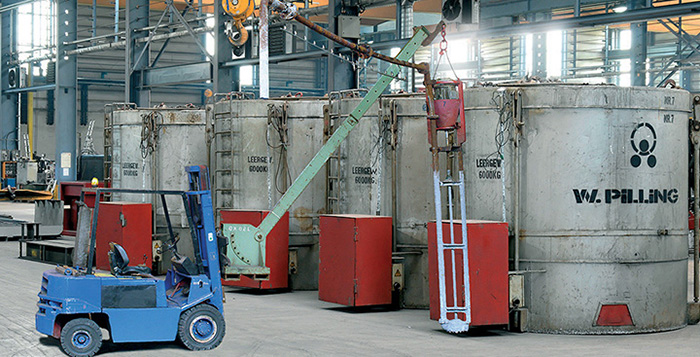
Galvanizing Kettle – Hot Dip Galvanizing | ANI METAL
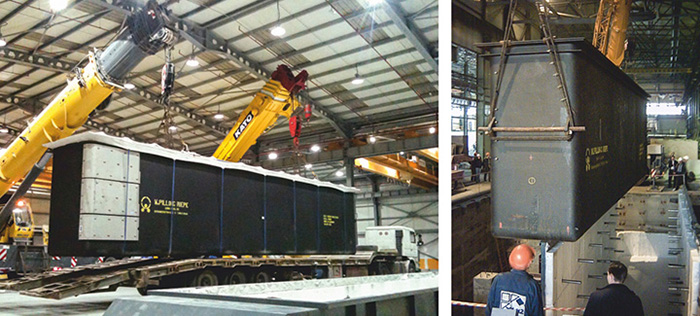
Zinc Pump Out – Hot Dip Galvanizing | ANI METAL
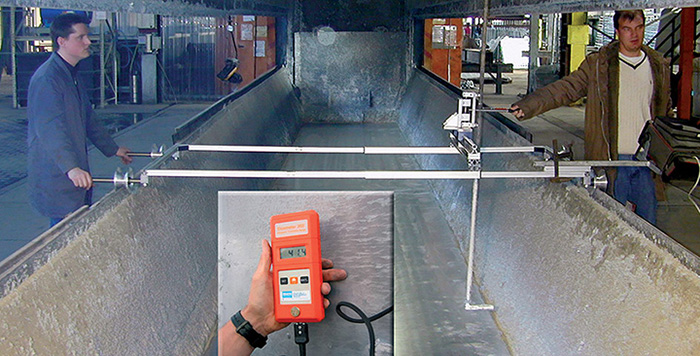
USI Measurement – Hot Dip Galvanizing | ANI METAL